Spiral mold to compare the flow characteristics of polymers
For both polymer processors and researchers, the characterization of the flow properties of polymer compounds is a crucial evaluation and due to its simplicity, the melt flow index (MFI) test is commonly used for this purpose. Sometimes, due to technical obstacles, such as thermal degradation during the MFI test, lack of material amount, or the presence of blocking fillers, MFI measurement cannot be conducted.
In this case, a spiral mold (Fig. 1) in an Xplore 12 mL Injection Molder can be utilized as a valuable tool for a comparative analysis of the flow behavior of polymer compounds at various processing parameters. In this technique, the polymer melt is injected into a spiral-shaped mold,and the distance the melt flows can be easily measured. The spiral mold is a valuable and straight forward tool that can be used to compare the flow characteristics of various polymeric compounds.
This quicktest also gives a good indication of the processability of the polymer compounds prior to actual production.
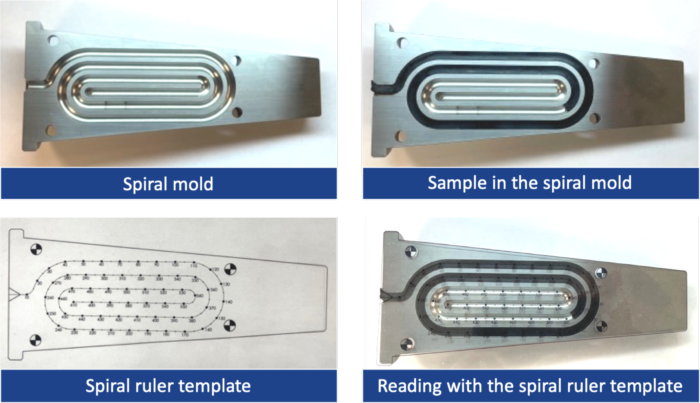
Long chopped fiber-reinforced thermoplastics(LFT), having the advantage of structural properties such as a good balance of mechanical properties and durability with relatively low cost, are widely used in automotive and other transportation sectors to replace metal parts. LFT materials contain longer glass or carbon fibers than short fiber composites that provide longer residual fiber length in the injection molded features with higher structural properties such as higher specific stiffness and toughness.
The flow behavior of LFT materials is difficult to obtain through MFI measurement since the long fibers buckle and block the die. Moreover, MFI measurement does not reflect the fiber breakage phenomena, which influences the flow behavior of the LFT. As a viable alternative, the flowability of LFT melts can be measured using the spiral mold method.
This study demonstrates that aspiral mold can be used to characterize the melt-flowbehavior of Polypropylene (PP)/glass fiber (GF) LFT compound. The correlation between the residual fiberlength and the flow properties is shown.
Glass fiber reinforced PP-based LFT pellets were provided by Sabic (Stamax30YM240) with an initial pellet length of 15 mm. LFT was melt processed in an Xplore MC15HT 15 mLmicro-compounder at 50 rpm screw speed. The amount of the LFT pellets at each charge was 12 g. Xplore IM12, a 12 mL microinjection molder, was used for injecting the melt into the spiral mold. The injection and holding air pressure was 6 bar, and the cycle time was 15 sec.
The residual glass fiber length is one of the factors that significantly influence the flow behavior. To demonstrate different residual fiber lengths, two different micro-compounding routes were applied. In the first route, called hereafter “direct,” to obtain longer residual fiber length, the recirculation valve was kept open. The material fed from the top hopper was allowed to pass one time overthe twin screws and directly extruded from the die to the transfer cylinder of the IM12 (Fig. 2). In the second route, to promote the breakage of the fibers, the valve was kept closed, and the melt was compounded (sheared) for 2 min. and then transferred to the IM12.
The effect of the barrel temperature and the mold temperature on the flow behavior was also investigated (Table 1). The flow length in the spiral mold was easily measured with a spiral ruler template, as shown in Fig 1.
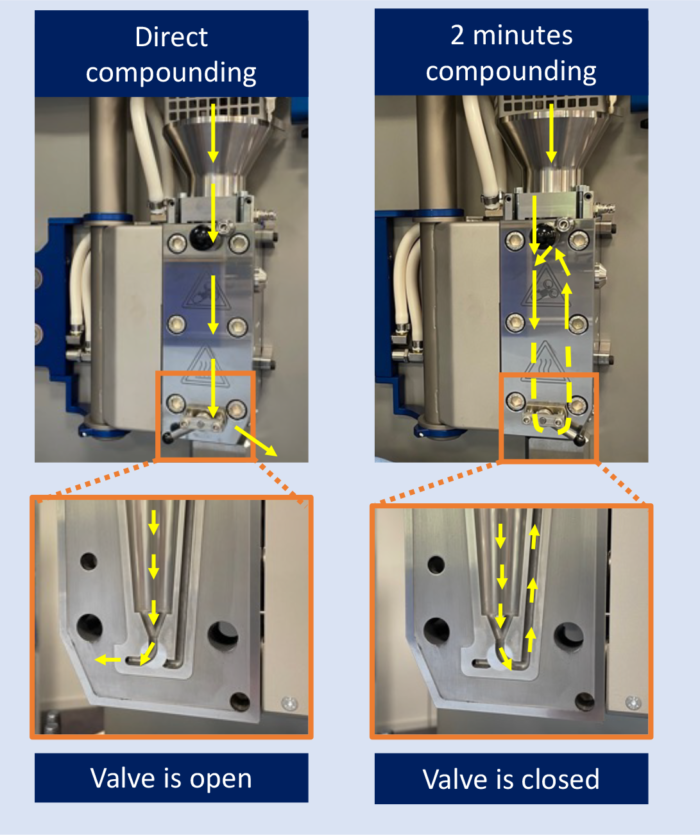
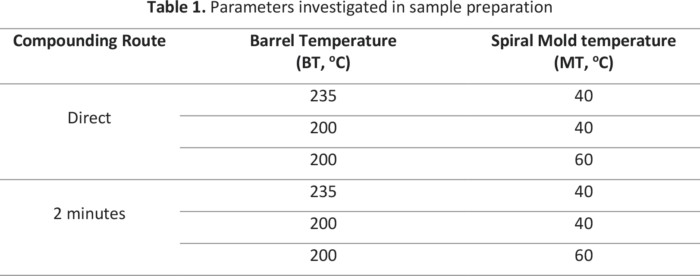
The change in the flow length concerning the three parameters mentioned above is shown in Fig. 3. The compounding time of 2 minutes results in a significantly higher flow length in the spiral mold for each given experimental combination. Increasing the barrel and mold temperature also yields a comparable rise in the spiral flow length.
It is known that the flowability of the glassfiber-reinforced thermoplastics isdominated by the residual glass fiber length. The glass fiberlength after injection molding was investigated to demonstrate the averagefiber length versus the flow length of the samples. Approximately 1,5 g of
injection molded composite material was pyrolyzedin a furnace at 600oC for 2 hrs to allow the removal of thePP matrix. Then the residual glass fiber reinforcement was analyzed under alight microscope (Fig 4). The average fiber length was determined using image analysis software.
The results showed that the average fiber length for direct compoundingis above 1000 mm and did not change significantly with the barrel and the mold temperatures. On the other hand, the samples compounded for 2 min exhibited considerably lower average fiber length (below 300 mm) since they were exposed to shear forces for alonger time.
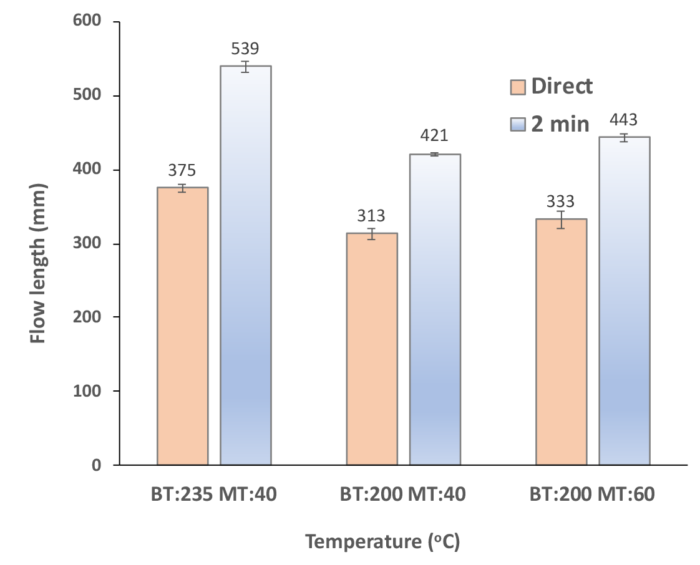
(BT: Barrel Temperature, MT: Mold Temperature)

The compounds having longer average fiber lengths revealed shorterspiral flow lengths. When the size of the residual glass fiber is longer, the capacity for hindering the molecules’ movement is more substantial; therefore,the melt viscosity will be higher. Moreover, when the residual fiber length is dramatically higher, possible fiber buckling also retards/hinders the matrixflow in the narrow channels of the spiral mold.
Besides the intrinsic properties of the compounds, the processing conditions play a crucial role in the flow behavior of the polymers in the spiralmold as well. For any given compounding conditions, it is demonstrated that increasing barrel and mold temperature resulted in longer flow lengths due toretarded solidification of the matrix in the mold, hence longer flow patterns.
In this application note, we have demonstrated that the spiral mold canbe a practical tool to compare the flow properties of polymeric compounds. The flow length in the spiral mold is a strong function of the processing parameters and is well correlated with the intrinsic structural properties ofthe polymer compound. This quick and easy measurement tool is also beneficial for optimizing the process conditions of polymers with just a few trials or comparing flowability between materials in different molding process settings.
For further information, contact our experts at Xplore Instruments BV.